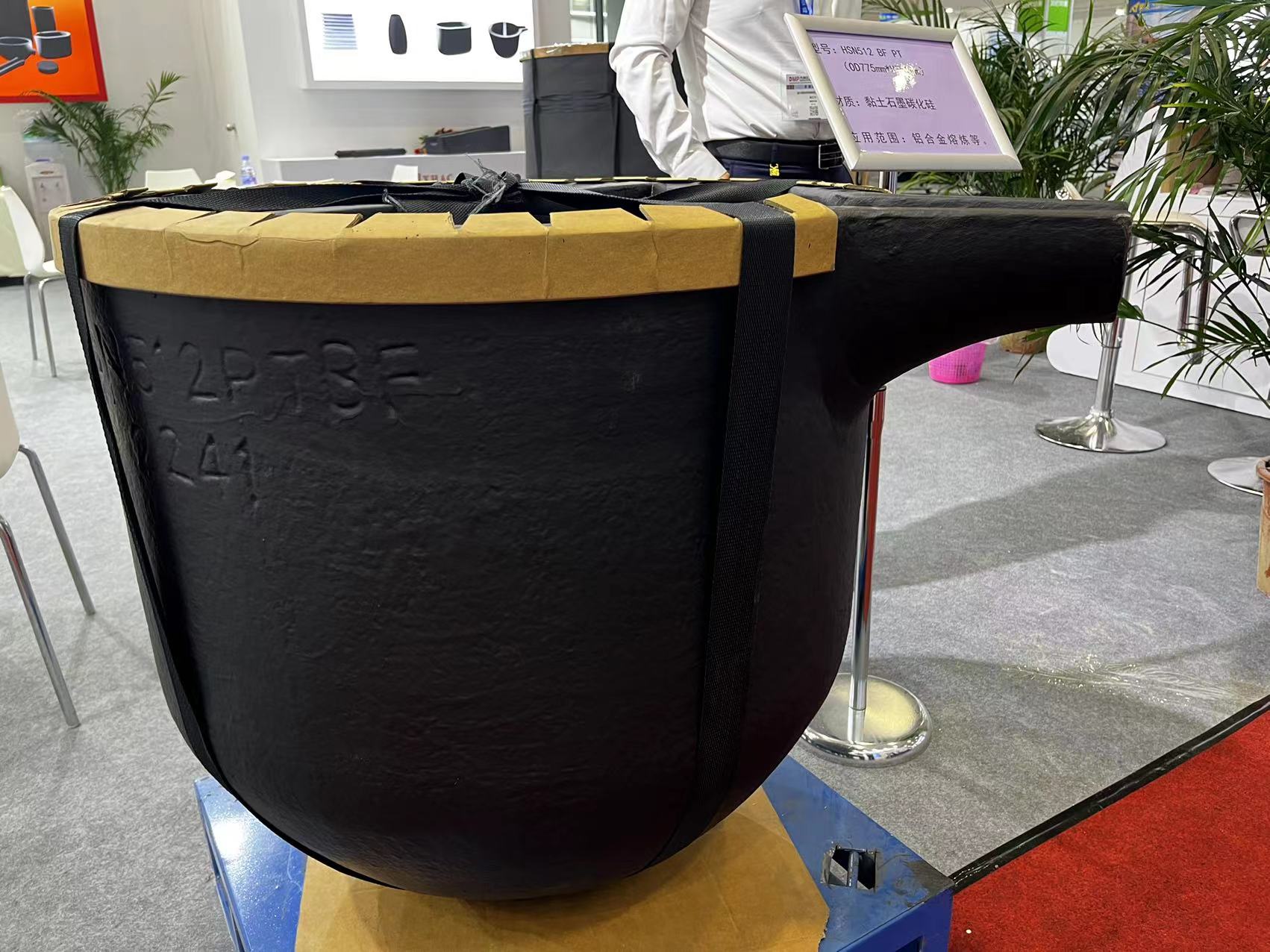
In de wereld van metallurgie en materiaalwetenschap,de smeltkroesis een essentieel hulpmiddel voor het smelten en gieten van metalen. Onder de verschillende soorten smeltkroes, vallen grafiet -siliciumcarbide (sic) smeltkroes op voor hun uitzonderlijke eigenschappen, zoals hoge thermische geleidbaarheid, uitstekende thermische schokweerstand en superieure chemische stabiliteit. In dit artikel zullen we ons verdiepen in het recept voor Graphite SIC-smeltkroes en onderzoeken hoe hun samenstelling bijdraagt aan hun opmerkelijke prestaties in toepassingen op hoge temperatuur.
De basisingrediënten
De primaire componenten van Graphite SiC -smeltkroes zijn schilfergrafiet en siliciumcarbide. Flake-grafiet, meestal 40% -50% van de smeltkroes, biedt een uitstekende thermische geleidbaarheid en smeerheid, wat helpt bij het eenvoudig afgifte van het gietmetaal. Siliciumcarbide, die 20% -50% van de smeltkroes uitmaken, is verantwoordelijk voor de hoge thermische schokweerstand van de smeltkroes en chemische stabiliteit bij verhoogde temperaturen.
Extra componenten voor verbeterde prestaties
Om de prestaties van hoge temperatuur en chemische stabiliteit van de smeltkroes verder te verbeteren, worden extra componenten aan het recept toegevoegd:
- Elementair siliciumpoeder (4%-10%): verbetert de sterkte en oxidatieweerstand op hoge temperatuur van de smeltkroes.
- Boor carbidepoeder (1%-5%): verhoogt de chemische stabiliteit en weerstand tegen corrosieve metalen.
- Klei (5%-15%): werkt als een bindmiddel en verbetert de mechanische sterkte en thermische stabiliteit van de smeltkroes.
- Thermohardende bindmiddel (5%-10%): helpt bij het binden van alle componenten aan elkaar om een samenhangende structuur te vormen.
De high-end formule
Voor toepassingen die nog hogere prestaties eisen, wordt een high-end grafiet crucibele formule gebruikt. Deze formule omvat 98% grafietdeeltjes, 2% calciumoxide, 1% zirkoniumoxide, 1% boorzuur, 1% natriumsilicaat en 1% aluminiumsilicaat. Deze extra ingrediënten bieden een ongeëvenaarde weerstand tegen hoge temperaturen en agressieve chemische omgevingen.
Productieproces
De voorbereiding van grafiet SIC -smeltkroes omvat een zorgvuldig proces. Aanvankelijk worden vlok grafiet en siliciumcarbide grondig gemengd. Vervolgens worden elementair siliciumpoeder, boorcarbidepoeder, klei en het thermohardende bindmiddel aan het mengsel toegevoegd. De blend wordt vervolgens in vorm gedrukt met behulp van een koude persmachine. Ten slotte worden de gevormde smeltkroezen gesinterd in een oven van hoge temperatuur om hun mechanische sterkte en thermische stabiliteit te verbeteren.
Toepassingen en voordelen
Grafiet SIC -smeltkroes worden op grote schaal gebruikt in de metallurgische industrie voor het smelten en gieten van metalen zoals ijzer, staal, koper en aluminium. Hun superieure thermische geleidbaarheid zorgt voor uniforme verwarming en vermindert het energieverbruik. De hoge thermische schokweerstand minimaliseert het risico op kraken tijdens snelle temperatuurveranderingen, terwijl hun chemische stabiliteit de zuiverheid van het gesmolten metaal zorgt.
Concluderend is het recept voor Graphite Silicon Carbide Crucibles een verfijnde mix van materialen die een balans van thermische geleidbaarheid, thermische schokweerstand en chemische stabiliteit bieden. Deze compositie maakt ze onmisbaar op het gebied van metallurgie, waar ze een cruciale rol spelen in het efficiënte en betrouwbare smelten en gieten van metalen.
Door het componenten en het productieproces van grafiet SIC -smeltkroes te begrijpen, kunnen industrieën weloverwogen keuzes maken voor hun specifieke toepassingen, waardoor optimale prestaties en een lange levensduur van hun smeltkroezen worden gewaarborgd. Naarmate de technologie vordert, worden verdere verbeteringen in de recept- en productietechnieken van Graphite SIC -smeltkrogs verwacht, waarbij de weg wordt vrijgemaakt voor nog efficiëntere en duurzame metallurgische processen.
Posttijd: Mar-12-2024