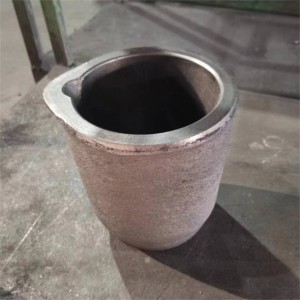
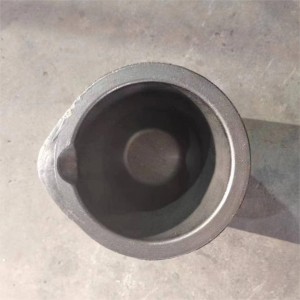
Er zijn significante verschillen tussenSiliconen carbide smeltkroesen Graphite -smeltkroes in veel aspecten zoals materialen, processen, prestaties en prijzen. Deze verschillen beïnvloeden niet alleen het productieproces, maar bepalen ook de effectiviteits- en toepassingsscenario's.
aanzienlijk verschil
Grapiet smeltkrommen zijn voornamelijk gemaakt van natuurlijk vlok grafiet en gebruiken klei als een bindmiddel. Deze combinatie geeft het grafiet smeltkroes uitstekende thermische geleidbaarheid en hoge temperatuurweerstand, waardoor het geschikt is voor toepassingen in smeltprocessen op hoge temperatuur. De unieke structuur en hoge thermische geleidbaarheid van natuurlijke vlok grafiet maken grafiet smeltkroes erg populair in de metallurgische en gieterijindustrie.
Siliconencarbide Crucible is gebaseerd op natuurlijk vlok grafiet, met siliciumcarbide als de belangrijkste component en hars met hoge temperatuur als bindmiddel. Als een superhard -materiaal heeft siliciumcarbide een extreem hoge slijtvastheid en thermische stabiliteit, waardoor siliciumcarbide -smeltkroes in meer harde omgevingen kunnen worden gebruikt. Het gebruik van hars op hoge temperatuur verbetert ook de algehele sterkte en duurzaamheid van de Crucible.
Procesverschillen
Het productieproces van grafiet Crucible is voornamelijk afhankelijk van handmatig en mechanisch drukken. Kleine grafiet smeltkrommen worden in het algemeen gevormd door mechanisch drukken, vervolgens gesinterd in een oven bij een hoge temperatuur van 1.000 graden, en uiteindelijk gecoat met anti-corrosie glazuur of vochtbestendige verf om de duurzaamheid en corrosieweerstand te verhogen. Dit traditionele proces, hoewel kosteneffectief, heeft beperkingen op het gebied van productie-efficiëntie en kwaliteitsconsistentie.
Het productieproces van Silicon Carbide Crucible is relatief geavanceerd, met behulp van isostatische dringende apparatuur en wetenschappelijke formule. Isostatische druktechnologie past uniforme druk toe (tot 150 MPa), wat resulteert in een hogere dichtheid en consistentie in de smeltkroes. Dit proces verbetert niet alleen de mechanische sterkte van de Crucible, maar verbetert ook de weerstand tegen thermische schokken en corrosie aanzienlijk.
Prestatieverschillen
In termen van prestaties zijn er significante verschillen tussen Graphite -smeltkroes en Silicon Carbide -smeltkroes. Grafiet smeltkroes hebben een dichtheid van 13 ka/cm², terwijl siliciumcarbide smeltkroes een dichtheid hebben van 1,7 tot 26 ka/mm². De levensduur van Graphite-smeltkroes is meestal 3-5 keer die van siliciumcarbide smeltkroes, wat voornamelijk te wijten is aan de superieure materiaalsterkte en corrosieweerstand van smeltkroes van siliciumcarbide.
Bovendien is het temperatuurverschil tussen de binnen- en buitenkant van de Graphite Crucible ongeveer 35 graden, terwijl het temperatuurverschil van de smeltkroes van siliciumcarbide slechts 2-5 graden is, waardoor het siliciumcarbide smeltbaarder is in termen van temperatuurregeling en thermische stabiliteit. De zuur- en alkali -resistentie en corrosieweerstand van smeltkroezen van siliciumcarbide zijn ook veel hoger dan die van grafiet smeltkroes, wat de energie -efficiëntie aanzienlijk verbetert en ongeveer 50% energie bespaart dan grafiet smeltkroes.
Prijsverschil
Vanwege verschillen in materialen en productieprocessen, hebben grafietcrinese en siliciumcarbide -smeltkroes ook significante prijsverschillen. Meestal zijn siliciumcarbide -smeltkroezen ongeveer drie keer duurder dan grafietpredigen. Dit prijsverschil weerspiegelt de aanzienlijke voordelen van siliciumcarbide -smeltkroes in termen van materiaalkosten, productieprocescomplexiteit en prestaties.
Samenvattend, hoewel siliciumcarbide smeltkroes meer kosten, maken hun superieure duurzaamheid, corrosieweerstand en energie-efficiëntie hen een meer kosteneffectieve keuze voor veel veeleisende toepassingen. Grapite -smeltkroes blijven op grote schaal gebruikt in veel traditionele toepassingen vanwege hun lagere kosten en goede basiseigenschappen. De respectieve voor- en nadelen van deze twee smeltkroes bepalen dat ze geschikt zijn voor verschillende toepassingsscenario's.
Posttijd: jun-13-2024